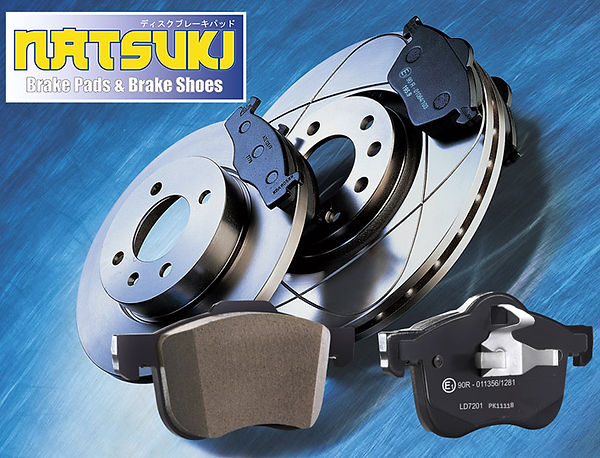
MATERIALS AND TEST REPORTS
Rotors are one of the important components of braking system which are usually made of gravy iron due to its superior damping (vibration absorption) and heat handling character. The combination of chemical combustion, physical properties and inferior microstructure for rotors identifies how quality and eligible product it is for the braking application.
Physical properties
According to SAE J431 G3000 standard, the automotive brake rotor and drum include specification as mentioned below:
-
Hardness (by Brinell hardness test): 189-248kgf/mm2,
-
Minimum tensile strength: 40,000 psi
Chemical composition G3000 grey iron:
-
Carbon 5.10%-5.40%
-
Manganese 0.75%-1.00%,
-
Sulfur Max 0.15%,
-
Phosphorus Max 0.15%,
Total Carbon equivalent of 6.15%-6.40
​
​
​
​
İnferior Microstructure
Pearlite microstructure = the graphite distribution and matrix structure of the Gray/cast iron.
​
This matrix should be predominantly pearlite: not more than 5% ferrite and less than 1% cementite.
​
The flake graphite form: Magnifications 100X
​
The one of core successes that we achieved with years of efforts was to be applied the ceramic high temperature advanced bonding technology into the material of NATSUKI brake products. We achieved that technology which pioneered the development of aluminium phosphate ceramics as a partial substitute for phenolic resin between in all over brake materials area, and supported the derivation of multiple ceramic-based formulations series as well. ​
​
The competitive formulation series of NATSUKI brakes include five types: Non-Copper Ceramic, Non-Metallic Ceramic, Low-Metallic Ceramic, Semi-Metallic Ceramic and High-Metallic Ceramic. These series of formulations were designed according to the requirements of different customers which demand our brake products by considering the effects of country condition during brake usage.
​
1. High-metallic ceramic-based formula series
Designed to be applicable for heavy commercial vehicles, van, bus, electric bus and any other similar vehicles. Features: Excellent high temperature duration (≥650°C), high structural resistance, sensitive braking and long product service life (approx. 40,000 km).
​
2. Semi- metallic ceramic base formula series
Designed to be suitable for light commercial vehicles, mini-vehicles, A-Class car/SUV and any other similar vehicles. Features: Perfect high temperature duration (≥550°C),nice structural resistance, sensitive braking, long product service life (approx. 40,000 km) and economic price.
​
3. Low- metallic ceramic base formula series
Designed to be suitable for various passenger cars, (especially) SUV and any other similar class vehicles. Features: Perfect high temperature duration (≥550°C), nice structural resistance, sensitive braking, good NVH performance and long product service life (approx. 40,000 km).
​
4. Non- metallic ceramic based formula series (including NAO)
Designed to be suitable for various middle or high-class cars and any other similar class vehicles. Features: Nice high temperature duration (≥500°C), nice structural resistance, sensitive braking, rotor friendly, dust free, noise free, excellent NVH performance and long product service life (approx. 40,000 km).
​
5. Non-copper ceramic-based formula series
Designed to be suitable for the vehicles which need to suit the market with strict environment regulation like European Union (EU) and North America (NA). Features: Perfect high temperature duration (≥550°C), high structural resistance, sensitive braking, environment friendly, dust free, noise free, rotor friendly, nice NVH performance and long product service life (approx. 40,000 km).
